
by Jennifer Kohlhepp | CM Magazine Featured
The Growing Demand for Digital Printing
By Dave Tushie, Magellan Consulting, Inc., ICMA Standards and Technical Representative
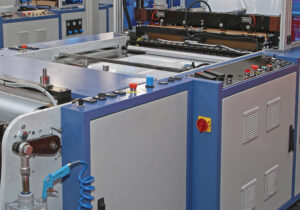
Digital printing in card manufacturing continues to see steady growth. Many, if not most, card manufacturers augment their lithographic (litho) and screen press operations with digital printing. Some use digital presses exclusively to print their cards.
Digital presses are known to have certain advantages over litho/offset presses in the following common production situations:
- Short production runs
- Prototypes of new card products
- Shortages in litho production runs
Most card plants running litho and screen press operations have a practical, economic, minimum threshold of cards per order. Usually this will run around 30,000 cards, minimum. Pre-press operations such as card design, brand/customer approval, plate creation and proof sheets are all time consuming and costly for short runs. Similarly, press setup and running of make-ready sheets are not efficient for short runs. Every card product has its own “recipe” in terms of four-color, spot/PMS color and related ink/water balancing for color consistency.
These issues are common for every short run litho/screen press job. Contrast these with related operational advantages cited with digital presses. These include relatively short job setup time, elimination of litho plates and making of screens, setup of a second job while the first is running, ability to combine traditional screen and litho passes into a single pass and registration accuracy on the sheet without shear cutting the edges. Even digital pre-press operations with a litho press, such as direct to plate engraving, only help narrow the advantages of digital press setup. The other operational performance advantages remain with the digital press.
The digital press can also be used to satisfy some of the demand for short turnaround situations where “safety” stocks of certain card products are inadequate or depleted. This has been seen when issuers have an unplanned mass re-issuance (e.g., a data breech) requirement in which neither their nor their card manufacturer’s safety stock is adequate. Progressive card manufacturers are using digital presses, with digital card products, that are matched to their litho card products, and can quickly start producing cards.
Some of the related advantages when using digital presses in these ways are the minimal costs in make-ready sheets (no, or little, substrate waste) and the positive impact on sustainability initiatives because sheet substrate waste is minimal.
Extending these advantages, some manufacturers are printing multiple card products on a single sheet, reducing the minimum threshold for a job size to one card. Others print limited graphics and variable personalization data, such as bar codes or serial numbers, on a single pass through the digital press. In an industrial setting, these machines can produce up to 30,000 cards per hour, and more!
However, limitations persist in certain printing effects and features common in many card products, despite continued developments in digital printing ink color gamut range and matching of PMS colors. True metallic inks, rainbow, guilloche and other forms of fine-line printing, for example, may be more suited to litho or silk screen printing processes.
Some other issues have surfaced in plants running litho, silk screen and digital presses in the card manufacturing processes downstream from the press room. Which jobs can use common collation, lamination, die-cutting and subsequent finishing operations when sheet sizes are different between the different presses? There are also a variety of technologies employed in different manufacturers of digital presses. How a card manufacturer envisions its use of a digital press in its overall manufacturing operations will impact the decision on which press is best suited for this purpose.
Large production runs and specialty films, coatings, colors, specialty inks and other considerations will continue to support the use of litho and screen presses. But digital printing will continue to grow and should be considered for most new equipment purchases. Knowing why and how digital printing can fit into your overall manufacturing operation can provide a more flexible and responsive business to your customers’ needs.
About the Author: David Tushie, ICMA standards and technical representative, has had a long and continuing career in the card industry, working for international companies such as DataCard, UbiQ and NBS Technologies. He has master’s degrees in engineering and business, holds U.S. and international patents in measurement and card issuance systems and has had several years of involvement with the ANSI, INCITS and ISO Standards process. ICMA is represented at six ISO and ANSI Standards Meetings through David’s standards role within the association.