Experts from the card manufacturing industry discussed the latest innovations and challenges in the lamination of smartcards and ID cards at the International Card Manufacturers Association (ICMA)’s recent CardTREX event in Heidelberg, Germany.
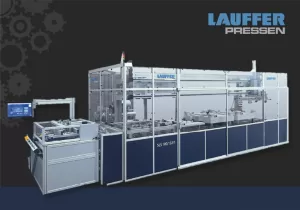
Uwe Postelmann, senior sales manager for lamination technology at Maschinenfabrik Lauffer GmbH & Co. KG, discussed various aspects of the lamination process that are critical to producing high-quality, durable and secure products.
Here’s a deep dive into the crucial factors and technologies shaping the future of lamination in the card and ID production industries.
Decisive Factors in Card & ID Lamination
The lamination process is a critical stage in the production of smartcards, ID cards and similar products, with multiple variables influencing the final product quality. Postelmann highlighted key factors that impact the lamination process:
- Quality Requirements of the Finished Product:
- High bond strength: Ensuring a durable and strong bond between layers.
- Minimal deformation: Preventing edge distortions during processing.
- Uniform thickness: Achieving consistency across the laminate, especially across large production batches.
- Surface quality: Ensuring the laminate is free from defects like scratches, stains or air bubbles.
- Yield: Maximizing output while maintaining quality, especially in high-security features like embedded windows or holograms.
- Testing compliance: Adherence to global standards like ISO/IEC 10373, which governs card durability and functionality.
- Influencing Factors During the Lamination Process:
- Pressure: Control over the pressure applied during lamination ensures uniformity and strength.
- Temperature: Consistent temperature control throughout the process is vital to prevent material distortion.
- Vacuum: Especially important for high-security cards, a proper vacuum setup can help eliminate air entrapment and ensure flawless lamination.
The goal of these processes is Total Process Control, where every variable is monitored and adjusted to ensure perfect lamination.
Simplified Card & ID Production Process
In today’s card and ID production lines, the lamination process is just one step within a larger production cycle. Postelmann illustrated a simplified process flow:
- Printing / Inlay / Tape Layer
- Sheet Collating
- Lamination
- Punching
- Personalization / Laser Marking
- Hot Stamping
- Milling / Embedding
- Inspection
This streamlined process minimizes potential delays and maximizes throughput, ensuring that high-quality laminated cards can be produced efficiently and accurately.
Types of Lamination Systems
Postelmann explained the different lamination systems in use today and how each caters to different production needs.
Conventional Lamination Systems (Single-Stack & Twin-Stack)
These legacy systems are still widely used, especially for mass production of cards and IDs.
- Key Features:
- High market penetration: These systems are well-established, with proven performance in high-volume production environments.
- Capacity: Can laminate up to 12 layers of sheets per press, with multiple press openings (typically 6-12 openings per press).
- Production Cycle: Cycle times typically range from 20-45 minutes, depending on stack configuration and the specific card material.
- Integrated Lines: These often include additional steps like collation, lamination and punching, all within one system.
Single Sheet Lamination (Quick Cycle Lamination)
Postelmann emphasized the cutting-edge nature of single sheet lamination systems, which are designed for faster processing and immediate quality feedback:
- Key Features:
- High flexibility: Ideal for R&D, product trials or processes requiring rapid adjustments.
- Faster Cycle Times: Lamination cycles can be as short as 45-90 seconds per cycle, offering a major reduction in production time compared to traditional methods.
- Minimal Consumables: Reduces reliance on costly consumables like press plates, which can be a significant cost in conventional systems.
- Real-Time Quality Control: Immediate quality checks after each lamination cycle, ensuring the final product meets high standards.
System Differences: Stack vs. Single Sheet Lamination
Postelmann compared the two main types of lamination systems, highlighting the trade-offs between capacity and flexibility.
Stack Lamination Systems
- High Production Capacity: These systems can produce up to 11,000 cards per hour in an eight-opening twin-stack configuration.
- Proven Technology: These are tried and tested technologies with high market penetration, offering stability and reliability.
- Longer Cycle Times: Lamination times are typically 20-45 minutes per cycle, making them less flexible for fast changes in product or process.
Single Sheet / Quick Cycle Lamination
- Faster Adjustments: This system excels in flexibility, with the ability to handle rapid changes in product specifications or material type.
- Real-Time Feedback: With a cycle time of just 45-90 seconds, manufacturers get immediate feedback on the quality of each sheet, ensuring that any issues can be caught and corrected quickly.
- Lamination Quality Control: Unmatched control over key variables like pressure, temperature, and flatness, ensuring superior lamination quality.
Concept Comparison
When comparing these systems, Postelmann outlined the pros and cons of each approach:
Conventional Lamination (Single-Stack / Twin-Stack)
- Advantages:
- High throughput and large-scale production.
- Low space requirements for each individual machine, but more space may be needed for other processes.
- Disadvantages:
- Medium flexibility: Longer cycle times (20-45 minutes) make these systems less adaptable to rapid product changes.
- Higher reliance on consumables.
Single Sheet / Quick Cycle Lamination
- Advantages:
- Unmatched lamination quality, with direct control over all lamination variables.
- High flexibility for product changes, ideal for smaller production runs or R&D.
- Disadvantages:
- Lower throughput: Production capacity is typically smaller, with a cycle time of 45-90 seconds per sheet.
Maschinenfabrik Lauffer continues to innovate in the lamination technology space, offering solutions that cater to a variety of production needs—from high-volume, low-flexibility systems to high-quality, flexible setups for quick turnaround times.
As the industry continues to evolve, commitment to precision and flexibility ensures that companies can adapt to the latest security and production demands in card and ID manufacturing.
More Insights on Card Trends
For more than 30 years, ICMA has represented the interests of the card manufacturing industry—which includes manufacturers, personalizers, issuers and suppliers—as its leading global association.
Throughout the year, ICMA members have the opportunity to share insights and knowledge by giving presentations during ICMA webcasts and events. The association’s main event is its annual Card Manufacturing & Personalization EXPO. The 2025 EXPO will take place from May 12-15 in Orlando, Florida.
ICMA offers regular educational opportunities, including ACE-Manufacturing, ACE-Personalization and ACE-Advanced Technologies training and exams at the ICMA EXPO. ICMA also offers ACE-Commercial training, which provides sales, marketing, customer service and other key personnel at ICMA member companies with the opportunity to learn the fundamentals of card manufacturing.
Learn more about the benefits of ICMA membership.