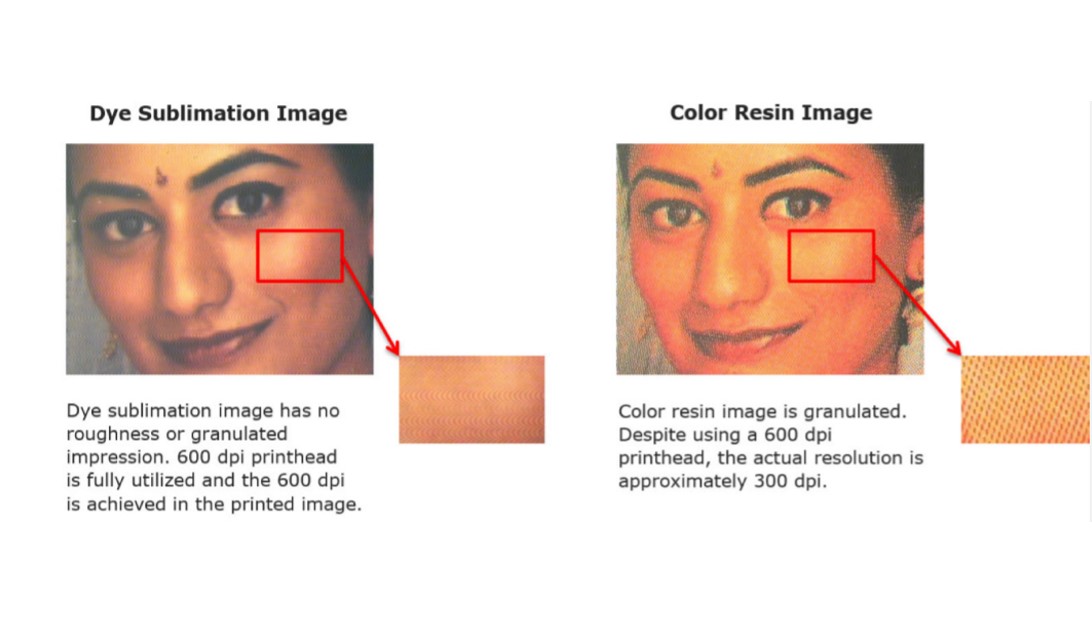
by Jennifer Kohlhepp | CM Magazine Featured
Selecting the Right Ink Technology for ID Card Printing
By Jim Meier, Senior Director of Product Marketing, HID Global
Organizations producing high-resolution identification cards have an array of card printers from which to choose. Understanding that not all print technologies are equal—and the basics of how they work—is essential to selecting the right solution.
Most identification cards produced today are still personalized using direct-to-card or reverse transfer color resin printing technology. Over the past decade, however, dye sublimation printing has become the leading color application technology of choice. It is a far superior application method than that of color resin and when paired with reverse transfer printing technology instead of direct-to-card printing, produces the highest quality images on the most durable cards. This is especially true for cards containing embedded technology such as proximity circuits, contact chips, or contactless integrated circuit chips.
Superior Image Quality
Dye sublimation printing creates various continuous tone colors within one individual dot or pixel of an image. It achieves this through a diffusion process that melds colors together into a smooth, continuous tone, and is capable of producing more than 16.7 million colors. Color resin printing, however, requires groupings of ink dots to signify one single color, lowering the resolution of the image. Illustration 1 below compares the resolution of dye sublimation printing to the resolution of color resin printing. Dye sublimation produces continuous tones that truly achieve the stated printhead resolution of the printer, either 300 or 600 dots-per-inch (dpi).
Color resin printing uses yellow, magenta and cyan to create only a limited range of colors as compared to dye sublimation. A single color is represented by a grouping of individual colored dots placed adjacent to one another. Even though resin printing may use a 600 dpi printhead, the actual quality of a color resin printed image remains only 300 dpi.
Images produced by dye sublimation technology are crisp and of realistic photographic quality. They achieve 600 dpi resolution by fully utilizing printhead capability. The dye sublimation process diffuses the dye, eliminating granulation while producing much greater image clarity. Dye sublimation printing diffuses the dyes together into a single dot on the card surface, producing higher levels of resolution than is possible with resin printers.
Color Comparisons
Color resin printing uses pigment-based colors while dye sublimation uses dye-based colors. As shown in Illustration 2 below, pigment inks do not accept light in the same way as dye inks. Dye inks focus light, while pigment inks reflect light. The larger size of pigment particles means they tend to scatter the light they reflect, which leads to less vibrant color. Small dye ink particles reflect light evenly for more vibrant color. Because of this, dye-based inks provide superior image color, and consequently, better quality images.
Some colors are not reproducible by color resin technology. Certain graphics, logos and precisely reproducible Pantone® colors are not available using color resin printing technologies. Specifically, Kodak Corporation stated that pigmented inks are less suitable for the simulation of Pantone® and specialized spot colors, which are especially popular in today’s corporate brand palettes. Better colors, plus the full gamut of actual colors, result in the highest quality print images.
Dye sublimation printing technology also utilizes color gradation more accurately. Therefore, images are clearer and better defined, allowing images with less contrast to be produced more accurately. This is important when creating small photographic images such as those typically printed onto identification cards.
Eye and Facial Recognition
Recognition of a person’s eyes is a crucial part of photo identification. Fine detail is more accurately reproduced with dye sublimation printing which gives greater resolution to the eyes (see Illustration 3). This enables convenient and accurate visual identification.
Full color reproduction capability is even more significant when printing a wide range of skin tones. One of the key reasons for using a facial image on a card is easy recognition of that person. Dye sublimation’s high color image quality is a crucial factor in getting the desired results of an identification card.
Printing Technology Methods
There are two primary methods of applying text and images to identification cards using dye sublimation technology—direct-to-card and reverse transfer.
In direct-to-card printing, images are printed directly to the surface of the card through heat and pressure. The printhead comes into direct contact with the card. This method is less than ideal when producing technology cards because the printhead is coming into direct contact with the uneven surface of the technology-embedded card.
In reverse transfer printing, images are first printed onto a clear film. Through heat and pressure, the film is then fused to the surface of the card. The printhead never comes into direct contact with the card surface. Technology card surface imperfections—such as smart chips that are not even with the card surface and ridges caused by internal RFID antennae—do not affect the print quality.
It should also be noted that cards produced with reverse transfer printing technology are innately more secure and durable than other types of cards because they are inherently tamper-evident—if a counterfeiter tries to peel apart the layers, the image essentially destroys itself. They also resist wear and tear by putting a durable layer of reverse transfer film between the card image and the outside world.
For enhanced card durability, protective overlaminates provide an ideal solution. For enhanced security, overlaminates can include holographic images and other Visual Security Elements (VSEs) resulting in credentials that are easy to verify but hard to duplicate.
Reducing Susceptibility to UV Fading
An overlaminate with holographic images can be adhered to a card using heat and pressure. Overlaminates are used to provide additional durability from abrasion, and add holograms and other security features, and protection against fading. Specifically, they effectively protect reverse transfer dye sublimation-printed cards whose dyes may fade over several years. Accelerated UV light testing of these laminated cards has shown fading is imperceptible to the human eye.
Another important consideration is the adhesion of the laminate to the card. Significant efforts have been made by overlaminate and reverse transfer dye sublimation manufacturers to ensure that the overlaminates remain securely fastened to the card. In a preliminary test on a limited number of color resin printing technology identification cards, the overlaminate did not remain securely fastened to the identification card.
In contrast, overlaminates that had been developed specifically to work with dye sublimation printed cards did remain securely adhered. With years of testing and field use, overlaminate failure on dye sublimation reverse image transfer cards has proven very unlikely (see Illustration 4).
Quality, Durability and Security
Reverse transfer dye sublimation printing technology is superior to color resin printing technology and is the clear solution of choice for technology-based identification cards. Not only does reverse dye sublimation printing technology deliver the best photo and text print quality, it ensures that finished credentials are durable and highly secure.
About the Author: Jim Meier is a senior director of product marketing with HID Global and manages the portfolio of desktop printer products. He has more than 25 years of experience working with printing technologies and has 20 patents related to these technologies.