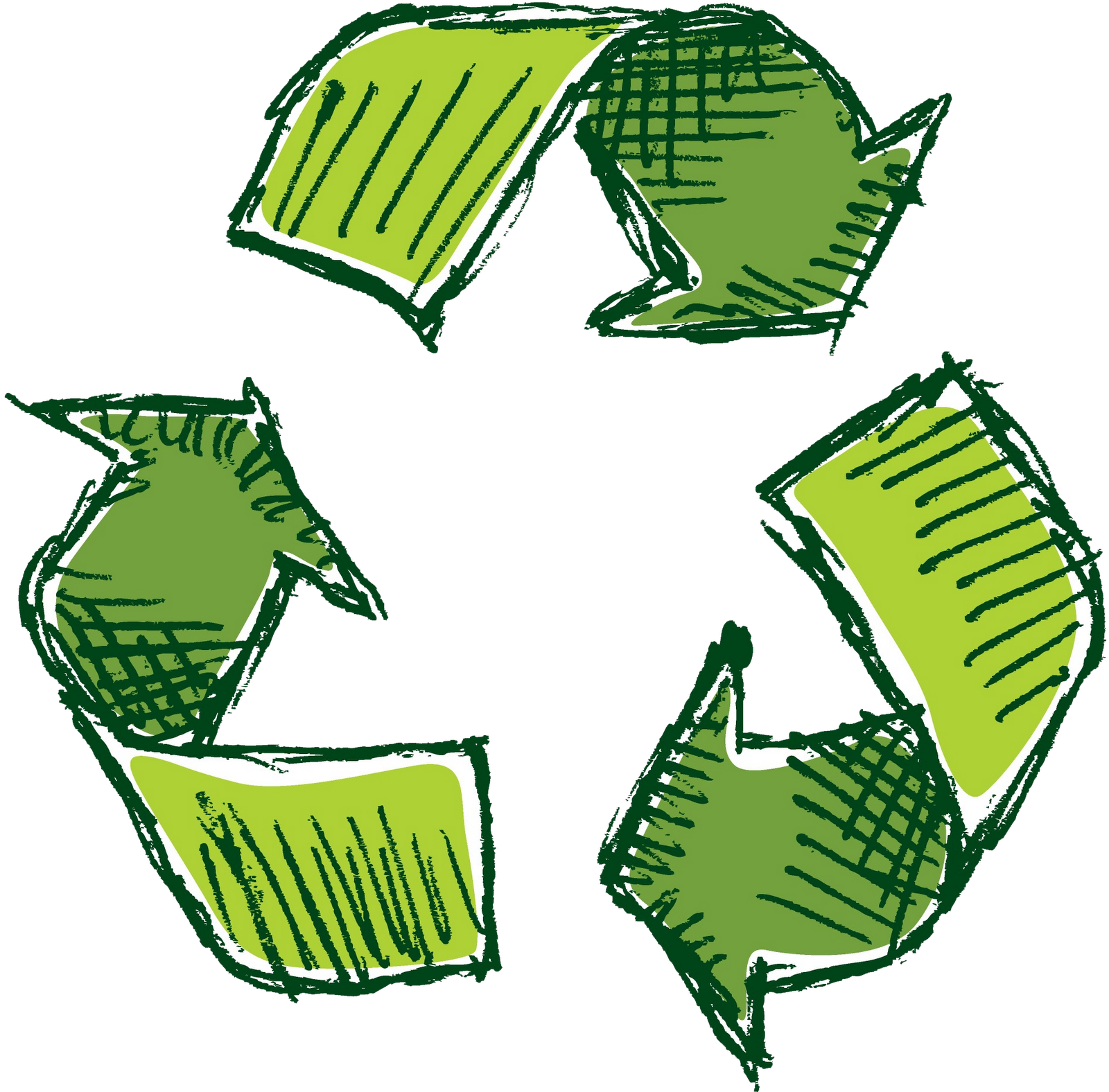
by Jennifer Kohlhepp | CM Magazine Featured
Demand Increases for ‘Greener’ Card Options
By Kimberly Tjoumakaris – ICMA Public Relations Manager
Consumers increasingly say they want brands that embrace purpose and sustainability.
And technology and social media have allowed consumers to easily promote or criticize companies for their green practices, or lack thereof.
Karen Brooker, vice president of sales at Plasticard-Locktech International (PLI), says businesses today are responding to the demands of consumers who are more educated and thoughtful in their approach toward going green.
David Tushie, International Card Manufacturers Associations (ICMA)’s standards and technical representative and CEO of Magellan Consulting Inc., agrees: “The heightened sense of interest in sustainable/recycled content is due to a greater sensitivity and awareness in general to climate change issues, but some is also due to better economic growth and a desire to contribute to the sustainability of the planet.
“Cards are highly visible to the consumer,” Brooker said. “When a card issuer reduces its impact on the environment with a change to card construction, the value of the brand is elevated in the eyes of environmentally conscious consumers.”
Corporate and community initiatives to reduce or eliminate single-use plastics have fueled the shift for some brands away from PVC to durable engineered paper.
PLI is experiencing increased interest in non-PVC plastics and paper substrates. “Paper can be a fantastic alternative for gentle-use cards and cards with a short lifecycle,” Brooker said. “But sustainable plastic resins are preferable for heavier-use cards, cards that will be exposed to the environment and cards that are intended to have an extended life.”
Sustainability Trends Shaping the Card Industry
New card designs may require card issuers to accept products that have different characteristics going to the user. For example, sustainable cards may be slightly lighter or have a different feel than the traditional product. More flexible cards may be mistaken as “light and flimsy”—dreaded adjectives for a card product in today’s market, which values a decided “thunk” factor.
“The greatest current trends seem to be increased use of metal cards (reduced PVC content) and plastic cards with recycled and/or reduced content,” added Tushie. “A lot of development work continues in alternative bio-based plastics like PLA and bioethylene PVC, but the widespread use of these materials is still somewhat in the future for card manufacturing.”
Overcoming Challenges of Going ‘Green’
While demand is increasing for greener card options, the industry still has several challenges to overcome before they become mainstream. The cards must be durable, secure and live up to the technological requirements of modern cards, which are no longer simple plastic rectangles.
A variety of options have been produced in the past, including paper-based cards, wooden cards and bioplastics, but these have mostly been for small manufacturing runs. None have caught up to the volume that petroleum-based plastics have.
Brooker says generally alternative materials come with drawbacks. For decades, card manufacturers have been engineering card products to comply with ISO/IEC 7810 and related international standards. However, products made from alternative materials may not fully comply. Recycled content films, especially recycled PVC, can present challenges to the film producers.
Finding an appropriate pre-consumer waste stream can be difficult. “There is often limited supply of suitable recycled materials, which runs counter to the card issuer’s desire for a high percentage of recycled content in the finished card,” added Tushie. “Recycled content often needs extra processing for successful film production, making the card more expensive than the standard product. Finally, contamination of the waste stream seems to always be an intermittent issue requiring the total purge of the supply stream and possible damage to manufacturing equipment.”
Brooker agrees and says one of the toughest challenges when dealing with alternative materials is getting a good bond between the layers that make up the finished card. “In traditional card construction, PVC layers form a chemical bond during lamination,” she added. “Non-PVC alternative materials may require the investment of significant research and development on the part of the manufacturer in order to achieve the minimum required bond and even a fully developed product is unlikely to have the bond strength and dependability of PVC.”