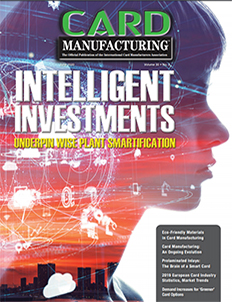
by Jennifer Kohlhepp | CM Magazine Featured
Intelligent Investments Underpin Wise Plant Smartification
By Jennifer Kohlhepp – ICMA Managing Editor and Kimberly Tjoumakaris – ICMA Public Relations Manager
Card manufacturing plant smartification can make factories more productive by increasing throughput, waste and expanding production floor flexibility. However, making the move toward an Industry 4.0 facility requires measured investments in technology, equipment and employee training and hiring.
Arroweye has invested $4 million to upgrade its plant to a smart factory in the past year. “Too many companies chase technology because they think it looks good or it’s cool or it’s a new feature,” said Peter M. Krauss, president and CEO, Arroweye. “But does it actually help streamline operations? Does that new software improve efficiency? A lot of people are realizing it didn’t.”
Invest in Smart Tech
Focused on how to do more with less, Arroweye evaluated what role technology plays in genuine manufacturing productivity efficiencies. “It’s not about getting rid of people,” Krauss said. “It’s about being able to scale your business and repurpose those people.”
Some companies chase efficiencies in hopes of removing workers from the payroll. “We haven’t taken that approach because our business is scaling and growing,” Krauss said.
Instead, employees whose jobs have become automated at Arroweye are offered opportunities to utilize their skills within other areas of the company “to add to our capacity and to add to growth,” Krauss said. “It’s helped our major efficiency gains and it has tremendously helped our business in the last year.”
The former president and CEO of PLI, Krauss grew that company from $15 million to $250 million. Impressed with Arroweye’s platform and technology, he started working there in April 2019. “When I came in, I wanted to make dramatic, sweeping changes to the organization,” he said. “Last year was our best year ever. We’ve invested nearly $4 million in equipment and we are making tactical changes to improve our actual workspaces and to position ourselves for success.”
Real-world smartification factory benefits, Krauss said, include increasing the speed of onboarding, implementing and executing new programs for clients as small as a local credit union or as big as a multinational bank. “Right now, during the coronavirus outbreak, we are seeing an uptick in business because if you go to a traditional printer and want to onboard a new program, their response is give us six to eight weeks,” Krauss said. “Our response is give us five to six days to onboard a new program. That’s the smartification and that’s this new technology. A lot of companies think they are doing it, but they aren’t.”
Arroweye has taken measured steps toward smartification. “As any business grows, it’s really easy to bolt stuff on; put stuff in,” Krauss said. “But when we take a step back, we ask is this the most efficient workflow, to move product through our pipeline, through our flow. We’ve spent a lot of time over the last few months reassessing that and making changes. We’ve already seen major improvements.”
The changes the company made in throughput, capacity and efficiency during its peak season last fall resulted in producing twice as much product with half the labor expense. “You do twice as much work without overtime, without working weekends and that reduces the labor,” Krauss said. “Now we have more capacity because those extra nights/weekends are freed up for new work. Every minute of every hour that you can fine tune your process helps you downstream. That’s how we started thinking about it—very gradually, incrementally.”
Plant smartification has become critical in the card manufacturing industry. “If you don’t do it, you risk becoming irrelevant,” Krauss said. “Clients are becoming ever more demanding; they want increasingly faster speed to market. And it will become even more important in the next six to 12 months as we work our way through the coronavirus recovery. Companies that can do things more quickly are the ones that will benefit.”
Invest in Tech-Savvy Employees
Card manufacturing plants have been hiring more tech-savvy employees in the past decade but the need for them is exponentially increasing with the growth of Industry 4.0. “The days of coming in, mashing a button and pushing out a widget…those days are done,” Krauss said. “Increasingly, production workers will have to become more tech-savvy. We screen for that during interviews with basic computer literacy
and skill testing. We look for practical and relevant experience. As we hire younger people…millennials get the bad rap, but they are the most savvy in the group—they are ready made for technology.”