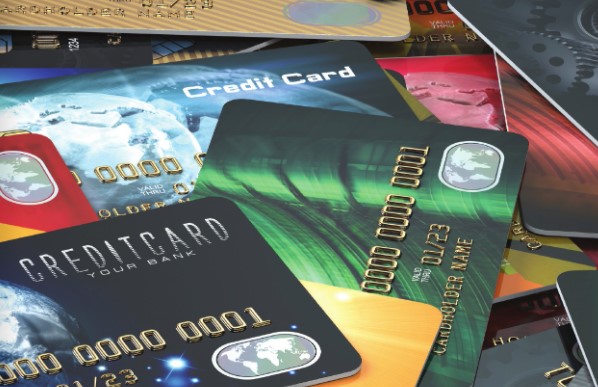
by Jennifer Kohlhepp | CM Magazine Featured
Card Creativity and Design
by Dave Tushie, Magellan Consulting, Inc., ICMA Standards and Technical Representative
Most of us have heard the adage “necessity is the mother of invention”. By definition, this is a creative process to produce something unique or “novel” from any predecessors. Often, the card design process is the application of known elements that can be brought together to create a unique product functionality. Let’s look at just a few examples (of the many that could be cited) in some current trends of card manufacturing to highlight this idea utilizing materials, manufacturing processes, security and technology elements.
PVC has been, and continues to be, the dominant card body material in the card industry. However, new materials continue to be developed and adapted for card manufacturing. More durable material configurations, such as composite layers of PET and PVC, are known for longer life requirements. Eco-friendly materials, including recycled PVC, PET/PETG and plant-based PLA, are available for those applications where planet-sensitive initiatives are paramount. Stainless steel, titanium and tungsten materials have all been adapted to card manufacturing, including full ranges of contact, contactless and dual interface cards. All of these, and many more alternatives, have been used or modified for specific card product purposes.
Sleek metallic finishes, dark uncomplicated, but elegant, designs with contrasting focal points and a colored core card edge are a current focus in graphic card design. Lithographic and silkscreen inks, separately and combined, can create desired graphic effects while adding, for example, needed security. Anti-duplication and machine-readable inks can provide such security while being used in the graphical design. Coordinating the graphic elements with the card body construction is a melding of card attractiveness with its intended functionality.
Security elements for cards continue to evolve as fraud and counterfeit attacks proliferate. Beyond inks, described above, card body designs and card personalization technologies continue to improve. For example, holograms and holographic laminates have long been used to protect high security cards from manipulation and forgery. Laser personalization can permanently mark the card body with cardholder specific data and images, including color photos. These elements can be coordinated with the card body construction and graphic design to achieve the needed security functionality.
Similarly, electronic elements continue to find their way onto, and into, cards. Biometric sensors, keyboards, buttons, displays and batteries are all routinely available to fit standard ID-1 configurations. For example, fingerprint sensors are now able to fit in a standard ID-1 dimension, without a battery required to power it. This capability will allow the authentication of a cardholder to the card credential itself, a big advance from today’s comparatively limited means of cardholder authentication using signature and PIN. Other functionality like displays for dynamic security codes or keyboards and buttons require batteries. This entails a card body construction with many more layers, and resulting complexity, than today’s most common card products.
Constant changes in card materials, functionality, graphic elements and personalization are just some of the challenges card manufacturers can expect. Creative solutions in design and manufacturing will continue to address these challenges. Keeping abreast of the new developments in each of these areas will allow card manufacturers to innovate as new card product requirements dictate.