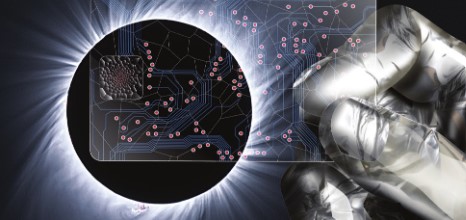
by Jennifer Kohlhepp | CM Magazine Featured
Card Manufacturing: An Ongoing Evolution
By Jim Hays – Business Development Manager, CPI Card Group
Retailers began issuing charge cards in the 1950s, which evolved to the first universal credit cards that could be used at a variety of establishments.(I)
Since then, the payment card industry has seen a lot of change. For example, there was a push in the 1980s to advance the manufacturing of credit cards to some lofty goals. A well respected leader in card manufacturing at that time said, “If we could just bring the card manufacturing process to a point where we could pour ink and plastic into one end of a machine and at the other end of the machine completed cards would pop out.” The reality is a lot more complicated than that! Let’s take a look at how some of
the steps in the process have evolved.
Prepress
Prepress transforms card art, copy and data into a format that is ready for mass reproduction. What used to be a manual and labor-intensive process has seen significant changes over the years. In the late 1940s, overlay systems were developed involving four-color proofs. Each of the process colors were on a separate sheet of clear film and then aligned or “registered” together into the final proof. Proofing was an operation with manual cameras and manual artwork that required stripping, cropping, sizing and fitting artwork into a specified real estate. Proofs were assembled by hand with clear acetate overlays showing each color separation along with the invisible UV association logos. It was believed that moving to a finished product without layers would never be accepted by the trained eyes of the designers and agencies that were scrutinizing these proofs.
Now we live in a world influenced by advanced graphic standards. In today’s world, software programs deliver color formulations, security features and dot patterns that are sensitive to gains and shrinkage. All of these things are more advanced than we could ever have imagined even 20 years ago. What once took days and sometimes weeks to produce the perfect proof, has now become minutes and hours.
Back in the day, prepared layered acetate proofs were sent through secured shipping to the customer for their review and approval or correction to be returned for either production or any adjustments. Today, this is accomplished through email and secured FTP services, directly to multiple locations for approval and returned the same way.
Printing Plates: ‘Step and Repeat’
Just as it sounds, the old way of creating printing plates one by one was a time consuming process. Negatives were produced for each color and a piece of equipment called a “step and repeat” was used to burn each color plate for each card cell to prepare for printing.
Now, digitally manipulated artwork and software-controlled color percentages result in an accuracy that is greater than the human eye can provide. Likewise, printing plates are burned (direct to plate) from a digital file, giving way to process speed and resolution improvements, which run circles around the “step and repeat” methods that were cutting edge at the time. Direct to plate was such an advancement of speed to print and a giant leap for quality.
Core Competencies
Cards printed on a solid core substrate that measured .026 inches thick have become divided. Initially, cards became a split PVC core using two pieces that measured approximately .013 inches thick and, more recently, cards were split again to make way for emerging technology to be placed inside.
Newcomers to the party include inlays, chips and proximity technology, which bring about a whole new set of challenges, such as learning to print on sheets that are as thin as 6 mil or less. New terms like “witness marks” and “key rolling” were introduced to describe the effects of the new embedded technologies within cards. The process moved from just printing a card to having specialized materials influence each step.
The other big change is the core color. In a plant 15 years ago, you would see pallets of white PVC as far as the eye could see. In today’s plants, you will see a rainbow of colors from red and blue to green and black. Again, this brought about more challenges; printing on white is straight forward, printing on red or green changes everything. Think back to primary school and what happened if you mixed red and blue together; the same principles apply.
Overlays: Collation and Lamination
The lamination process historically had a “bad boy” reputation in card manufacturing because it’s where color shifts and image distortion happened. Overlays are essential to protect cards from friction, scratches and the effects of UV sunlight. It’s almost hard to believe that at one point the collation process was manual with the operator aligning the front and back printed layers with the overlay laminates, by eye, and into the proper sequence, registration and thickness. Soldering irons tacked the layers together prior to putting them into the lamination machine. There was a single tower for heating and cooling.
Today the recipe book has evolved and the options of temperatures, time cycles and stabilizing pressures have been perfected, yielding the highest quality in the shortest process cycles. Machines work through a stack of printed sheets assembling and collating them using auto optic registration. They also introduce overlay films simultaneously, with the magnetic stripe materials pre-applied to the back. This one improvement has significantly reduced scrap, throughput and card quality.
Not only have recipes and processes evolved, so has the equipment. A single tower is used for heating that auto transfers to another single tower for cooling. Printed sheets are heated and cooled in minutes, where in the past it took hours.
From Sheets to Cards
One of the first card plants in the United States to have an optical punch for card cutting invited some of its competitors in to see the equipment and appreciate the advantages it brought. The owner believed that sharing the latest innovations would keep manufacturers motivated to always be on the cutting edge. It’s no wonder that manufacturers were eager for advancement, as the old way made for much waste. Sheets were sent through a guillotine to be cut down to strips or rows and then the rows into single cards resulting in rectangles without rounded edges. It also produced printed cards where the
printed information wasn’t to the card edge, which made for much waste. A tool that looked much like a pancake spatula carefully positioned the cards into stacks of 50 to be manually moved into a power-motorized cutter die where length, width and rounded corners were established.
Today, registration quality has been engineered into our processes by printing fiducial indicators on the sheets, allowing for optical registration for a male and female die cavity to punch each card from the sheet with the highest registration possible.
Magnetic Stripe
The magnetic stripe made its debut in 1969(II), but it wasn’t until the 1980s that it became mainstream on financial cards. IBM® proudly named the magnetic stripe one of its top 100 contributions to society(III). Like a ribbon, the magnetic stripe was rolled onto each card, as they traveled down a conveyor belt or track.
Now, in an effort to improve application speed and durability, magnetic stripes are laid onto the rear overlay in sheet rolls and then introduced during the collation process as a subassembly, as mentioned earlier. The stripe is laminated onto the card during the lamination process, resulting in a much more durable stripe. The magnetic stripe technology itself has advanced as well. Introduced as a low-coercivity (lo-co) magnetic stripe in a two, three or four track format, had its difficulties. Magnetic information on the stripe was often lost or destroyed by consumer use.
Cue the introduction of the hi-co mag stripe. The primary difference between the lo-co and hi-co stripe was the level of difficulty it took to encode and erase the information on that stripe. The stronger the magnetic field (2750 Oersted), the more durable and less likely for information to be erased.
Four decades after its creation, the credit card magnetic stripe, which may have revolutionized the way we use credit cards, might be seeing the end of its day. Many countries do not use the magnetic stripe at all, except as a fall back to prevent loss of the sale. They are now using either chip and pin or contactless “tap and go.”
EMV® Chips: Complexity Times 10!
The industry had card manufacturing down pat and then a two-stage pocket needed to be drilled into the front of the card at 25 thousandths+ deep without breaking through to the card’s back core, but the challenge of milling the complex pocket was only the beginning. There was also receiving and inventorying chips by size and color of contact plate, chip type, software application(s) and a cryptographic key.
Manufacturers need to manage the lifecycle of the chip/mask/applications and use up all the card stock by the allotted date to avoid waste. Clients need help managing card stock to ensure that when they are ready to upgrade chips, the move occurs before expiration and the cards are delivered to customers before the chip’s end date.
Past Leads to Future
In working with some of the best and brightest, there have been those who have created and provided amazing, cutting-edge products for this industry. But, it’s not over. Be sure your seatbelt is low and tight and be ready for the future because more changes are likely to come.
EMV® is a registered trademark in the U.S. and other countries and an unregistered trademark elsewhere. The EMV trademark is owned by EMVCo LLC.
I Cothern, Lance, et al. “When Was the Credit Card Invented?” Credit Karma, 17 Sept. 2019, www.creditkarma.com/credit-cards/i/credit-cardhistory/.
II “Magnetic Stripe Technology.” IBM100 – Magnetic Stripe Technology, www.ibm.com/ibm/history/ibm100/us/en/icons/magnetic/.
III IBM100 – Icons of Progress, www.ibm.com/ibm/history/ibm100/us/en/icons/.
About the Author: Jim Hays is a business development manager for CPI Card Group. He is responsible for direct and reseller sales, focused on secure cards, personalization and manufacturing across medium and larger issuer clients. His experience in the card industry spans nearly 32 years, working for and supporting leading companies in financial and technology services. Hays joined CPI
supporting operations in quality, procurement and sales and has advanced his skill set within secure card manufacturing by earning ICMA ACE-P and ACE-M certifications.