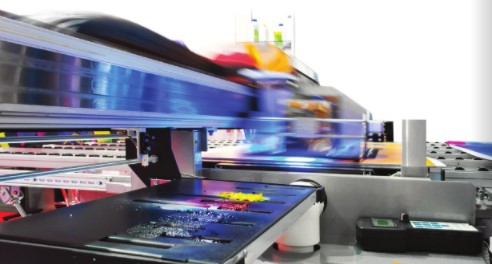
by Jennifer Kohlhepp | CM Magazine Featured
Not All Cards are the Same: The Subtleties of UV Ink
By Roy Kropman, President, Buskro
Ultraviolet (UV)-curable inks have long been described as being versatile and are often touted as being compatible with virtually all printing substrates. While this statement is mostly accurate, it is important to note that the performance of UV inks is not a panacea for all your card printing requirements.
Achieving a streak-free image that is largely scratch-resistant requires that you pay attention to and consider a number of factors including dosage and irradiation of the UV light source, the surface tension of the material, ink drop volume and print density and ink formulation.
Although choosing and working with materials that are conducive for inkjet printing is critical for success on plastic cards, you also have to focus on those features and tools inkjet printers and UV LED curing solutions offer in achieving optimal print results for your variable data printing needs.
LED Curing Lamp Irradiance and Dosage
UV ink exposure to light and the amount of ink deposited determines the level of cure of the printed image. When there is insufficient LED light dosage or too much ink, a “wet” or partially cured image with poor scratch-resistance or adhesive properties is the outcome. In cases where the printing application requires high-speed and/or high-density (high dots per inch (DPI) images, conditions that stretch the limits of curing, it may be necessary to augment light dosage by extending the exposure period with lamp rotation or by adding curing lamp capacity. LED curing lamp solutions that are equipped with a minimum intensity of 16 w/cm2 are sufficient for most applications.
Surface Tension
The dyne level of a material is called its surface energy and the general rule for the optimal application of UV inks onto materials is that the material’s dyne level exceeds the ink’s dyne level by at least 10 dyne. A material’s surface tension is a function of its coating properties and the time elapsed from production. In most cases, a material’s dyne level will often decrease over time which means a material that exhibits good adhesion shortly after its manufacture may produce less predictable results a number of days afterwards. If this is not taken into consideration before printing, it can negatively affect the print quality and result in product waste.
When there is an imbalance between the ink and the printed material’s surface tension, adjacent ink drops deposited on the material may not flow freely and join the rest of the ink mass causing an image to have a streaky appearance in the best case or easily removed (through abrasive contact) in the worst case. Glossy printed materials including some plastic cards, UV-coated and aqueous-coated stocks can be challenging. One way to create optimal print conditions is by altering the material’s surface properties with a surface treatment device such as corona, plasma or heat; another is choosing an ink formulated with good wetting properties.
Ink Formulation
Not all UV inks are the same. UV inks contain a number of components in varying amounts including monomers, oligomers, photoinitiators, pigments and additives, which can be adjusted to impact certain characteristics including wettability and adhesion. That’s why choosing and working with an ink that exhibits good wettability is critical to achieving a print image that adheres and is streak-free. There are inks specially formulated for the plastic card industry.
Drop Volume and Drop Density
Overcoming image streaking is achieved by either applying a sufficient volume of ink, employing an ink with good flow characteristics (wettability) or a measure of both. When considering ink volume or more precisely ink density (image resolution X drop volume), modern inkjet technology offers an assortment of possible solutions either by a combination of high-resolution (600 X 600) and smaller drops (6-14 pl) or via a more moderate resolution (400 X 600) combined with a large drop (30 pl). Keep in mind that vertical DPI is a feature of the printhead and cannot be changed while horizontal DPI can be set by the operator but does impact top-end speed.
To ensure your success when inkjet printing on plastic cards, use LED curing lamp solutions equipped with a rotating lamp, a choice of print technologies offering a variety of resolution and drop volume combinations and an ink specially formulated with good flow properties.
6 Things to Remember:
- High print speeds decrease light exposure time while high-resolution images require more light dosage. Choose a high-power curing lamp solution with an ability to extend exposure time via lamp rotation.
- Material surface tension may be a challenge and be adversely affected over time. Choose an ink formulation with good wetting properties.
- Produce streak-free images by depositing a sufficient amount of ink. Choose a print solution designed either as a high-resolution (600 X 600) and small drop (14 pl) model or medium resolution (400 X 600) and large drop (30 pl) model.
- Printed images cure from the surface inward and continue to cure over time.
- Optimal surface tension range for most material is around 38-50 dynes, but should not be higher than 54-60 dynes.
- Surface treatment devices such as corona, plasma or heat act to alter the surface tension to make it more ink-friendly and optimize surface tension prior to printing.
About the Author: Roy Kropman is the president of Buskro, but prior to becoming president he was part of the company’s engineering team. He has a degree in mechanical engineering and is still heavily involved with the engineering projects. He has been at Buskro for more than 30 years. The majority of the content in this article comes from years of testing different inks and methods to provide the best possible print for UV inks on plastic cards.