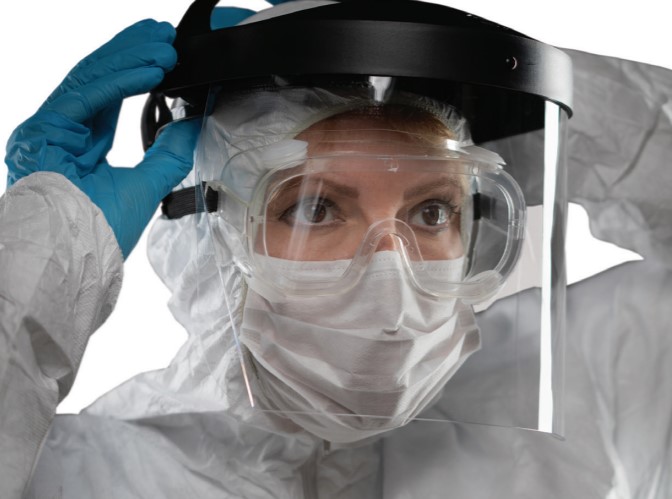
by Jennifer Kohlhepp | CM Magazine Featured
Card Manufacturing Plants Pivot Operations Amid COVID-19 Pandemic
By Kimberly Tjoumakaris, ICMA Public Relations Manager
The COVID-19 pandemic has caused business interruptions across the globe and it is likely these disruptions will continue until there is a vaccine or herd immunity.
Some card manufacturing plants have adapted to the new business landscape by restructuring their product offerings to remain operational. Bristol ID Technologies moved beyond producing cards to manufacturing face shields. The company also explored making card sanitization stations for the hospitality industry, as well as microbial card coatings.
Bristol ID Technologies also used downtime during the pandemic to accelerate new projects. “We do not have a designated research and development (R&D) department or equipment,” said Keith Yeates, CEO of Bristol ID Technologies. “We took advantage of the lull in production to use our equipment to work on new R&D projects.”
Similarly, Variuscard, a European card manufacturer, pivoted operations and invested in new hardware, such as a digital cutter, to manufacture face masks and face shields. As of press time early in July, 50% of the company’s revenue could be attributed to non-card products.
Klöckner Pentaplast shifted its operations globally to supply plastic for face shields, virus detecting test equipment, food packaging and signage production.
The pandemic highlighted the necessity for supply chain diversity, which allows card manufacturers to swiftly respond to changing market demands and customer needs. Bristol ID Technologies experienced some supply chain delays with materials coming out of Asia, which forced the company to evaluate inventory levels.
“If there is a strong rebound in certain markets, we want to be prepared,” Yeates said. “To minimize the future impacts due to another crisis or pandemic, it is so important to have at least one alternative source for every product.”
Similarly, when borders shut down in Europe, card manufacturers had difficulty transporting materials. “We have two suppliers for all of our raw materials. For example, our main PVC supplier is in Italy and our secondary supplier is in China,” said Michael Dorner, CEO of Variuscard. “COVID-19 has taken our risk management strategy to a completely new level. When the pandemic hit the world at the same time—that was something we could not have anticipated. Not having access to certain products, such as isopropyl alcohol, is a very new problem that we haven’t had to tackle before.”
Klöckner Pentaplast ensured raw material sourcing and continuity through its worldwide supply chains. “We have a sophisticated supply chain, which allows us to effectively and efficiently balance purchasing and production throughout our world network,” said John Schneiderhan, product manager, cards/graphics Americas at Klöckner Pentaplast.
Variuscard continues to monitor its stock very carefully with a goal to remain as flexible as possible. “We don’t know how or when the market will rebound,” Dorner said.