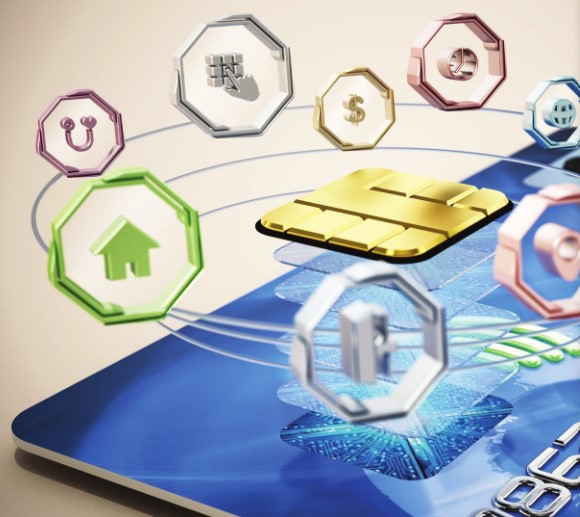
by Jennifer Kohlhepp | CM Magazine Featured
Prelaminated Inlays: The Brain of a Smart Card
By Clothilde Manzano PhD, Marketing Development Manager, Ahlstrom Munksjö and Jessy Khairallah, Founder and Managing Director, Neksta
When looking at the card industry worldwide, contactless smart cards are on the rise and becoming the preferred solution for many applications. Those smart cards contain added-value attributes from embedded electronics to security features to fingerprint sensors and special materials…and are no longer simple plastic cards.
A wide variety of smart cards are in use today and the complexity of their production process depends on the industry and application requirements (banking, identity, transport, etc.). To adapt to new demands, card and inlay manufacturing processes have evolved over the past 10 years.
Inlay production is one of the first steps required to manufacture a smart card; usually overlooked, it constitutes creating the core and brain of the final card and should get more attention.
The hidden brain of a smart card
Called a pre-laminated inlay or Prelam®, an inlay is a product integrating an electronic device within a sheet carrier. Single layers with embedded electronics are fused together under pressure and temperature during the lamination process to form one homogeneous and durable sheet carrier.
The various manufacturing steps to produce an inlay are much more complex than meets the eye. On one hand, you have unique processes; on the other hand, you mix different design combinations and various variables in order to be compliant with the technical requirements and final application standards. Think about different materials, sheet layouts, thicknesses, antenna technology, chip module connections, security feature integration, mechanical and functional requirements, etc.
In the end, the quality of the inlays will determine the end-product quality. Dimensional precision and radio frequency accuracy are two of the main checking points. Paying attention to the manufacturing steps, and more precisely to lamination process optimization, is key for inlay quality and productivity.
The lamination process
One of the most critical steps in inlay manufacturing is the lamination process. Lamination is a science but also an empirical art because of the many variables that come into play to obtain a repeatable and qualitative product. While the equipment varies from one manufacturer to another, the methodology and process definition setup are more or less the same for a defined product.
Prior to setting up any lamination parameters and fine-tuning design, one step is often overlooked by manufacturers. Indeed, lamination accessories must be considered. Pads, cassettes and metal plates are lamination accessories ensuring inlay and lamination output. Checking their quality and condition is recommended to increase performance and production efficiency.
The inlay surface replicates the plate surface. Any defect or irregularity on the plate is transferred onto the inlay. Since both sides of the plate come into contact with the inlay, both sides of the plate need to have the same quality level. On the other hand, the pad offers controlled heat and pressure. These accessories—lamination pads, cassette and plates—have a lifespan and their condition and maintenance will weigh heavily in the lamination outcome.
The release sheet
When it comes to increasing the lifespan of the lamination accessories and optimizing the lamination performance, an additional accessory can be used: the release sheet. A release paper sheet—or parchment—would be inserted between the inlay and the metal plates.
This release paper sheet plays the role of a protective layer to prevent the risk of electrostatic discharge of the chip, as well as to reduce contamination and visual defects that could be transferred from the plates onto the inlay surface. One side comes into direct contact with the metal plates and reduces the risk of damaging their surface and as a result increases their lifespan.
As well as setting up the right lamination parameters and technical features, it is important to pay attention to the lamination accessories and consider the use of a release paper sheet, which will add valuable benefits to the manufacturing inlay process and contribute to the productivity efficiency.
Conclusion
A good quality prelaminated inlay is the crucial starting point for card makers to manufacture a good end product: a functional smart card. Lamination is one of the essential processes in the production of these inlays. The key to a successful lamination lies in establishing the right balance between all the different variables: from the product design, equipment type, accessory setup and condition and loading method to fine tuning the recipe parameters. Getting this balance right will maximize productivity, improve the yield, reduce scrap and lead to a repeatable qualitative product. In particular, lamination accessories deserve their share of the limelight. Indeed, imperfection or defect on the inlay sheet can impact the process and product of the card manufacturing.
About the Authors: Clothilde Manzano is the marketing development manager at Ahlstrom Munksjö. A global leader in fiber-based materials, Ahlstrom Munksjö supplies innovative and sustainable solutions to its customers and aims to expand the role of fiber-based solutions for sustainable everyday life. For more information, visit ahlstrom-munksjo.com. Jessy Khairallah is the founder and managing director of Neksta, which specializes in technical support and solutions for the smart card and RFID industries. For more information, visit neksta.com.